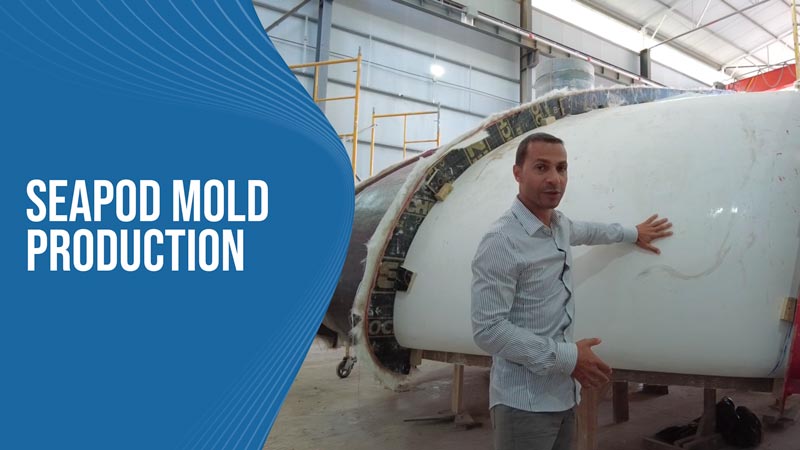
We are making progress on the molds for the shell of the SeaPod. Here we have the positive mold, or plug, which we have been working on for about a year. This will be the exact shape of the final product.
Each of the 14 sections is prepared separately first with a layer of tooling gel, which will create a very hard surface that will give the negative mold the durability required for repeated use. It also creates a surface that can be sanded and smoothed effectively to ensure that the final SeaPod has a perfect surface.
On top of the tooling gel, we are applying a layer of fiberglass and resin followed by crosspieces to reinforce the mold for strength and longevity. Once the entire SeaPod mold has been layered and has finished drying and setting, each section will be pulled off.
When all of the sections are completed and removed from the plug, we will have a complete mold for our SeaPod which will allow us to start building the shells. The process of creating the molds takes about three to four weeks, but it is reusable and it will increase the speed at which we can produce shells.
A fully completed mold will allow us to create a shell for our SeaPod in about two weeks. As we create more molds, we will be able to scale production and create shells on a regular basis. This process sets the stage for our SeaPod shell construction and will allow the interior work to begin after our shells are completed.
This is an important step towards delivering finished SeaPods and it takes us closer to the goals that we have in mind. We are working hard to reach these goals while keeping sustainability and efficiency in mind. There are more updates to come from Ocean Builders, so make sure to stay tuned!