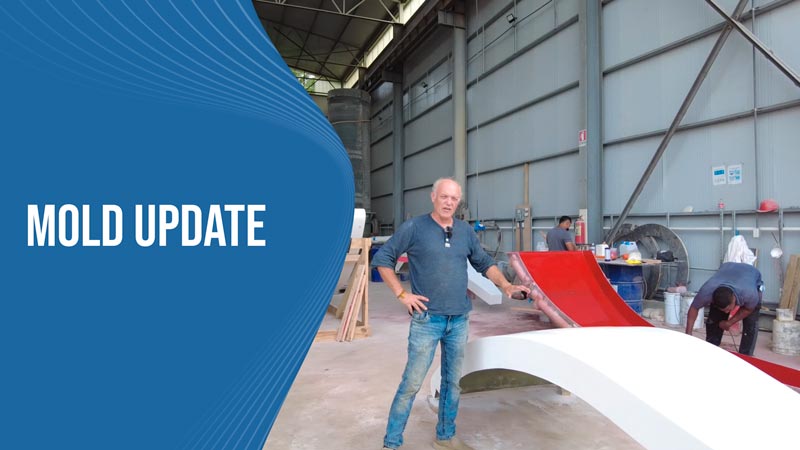
We are back at the Ocean Builders factory with another update on the progress of our molds. As you can see here, we have just successfully removed another subfloor section from the mold. Our employees are finishing up some polishing on the surface of the tooling gel coat which will be used again to make more sections.
Before we make the sections, we cover the tooling gel surface in a layer of releasing wax which helps the section release from the mold easier. We have to remove any residual wax after producing each section so that we can keep our surface perfectly smooth and avoid any wax buildup that would deform our sections.
Once we remove all of the wax, polish the surface, and reapply a new layer of wax. We then start applying the layers of fiberglass to the mold. Each section is made of seven layers of fiberglass which when cured, will be popped out of the mold and have the shape needed for our subfloor sections.
The durability of these molds is very important. We need these molds to be durable enough to withstand repeated use. These subfloor sections are a good example of why we use the tooling gel coat to give us a strong surface that can be used over and over. We will need 26 of these subfloor sections for just one SeaPod, so you can see how many sections we will be making when we are producing SeaPods on a regular basis.
We will make several molds so that we can make multiple sections at once, making the entire process move along much more quickly. Working out the kinks and refining our process is crucial during the building of our first few SeaPods so we aren’t necessarily trying to pump them out as fast as possible just yet, but things are coming along nicely and we will be going full speed soon!