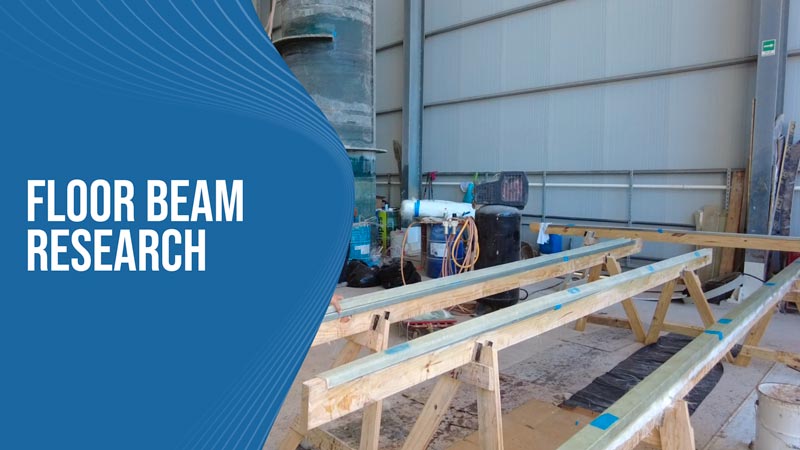
At the factory, we have been doing a bit of testing on our floor beam designs. The beams are made of fiberglass which will give us the strength required to be safe while keeping things as lightweight as possible.
We start the production of the floor beams by laying two layers of fiberglass cloth along a steel beam. Once we roll the epoxy onto the cloth and let it dry, then we can remove the rigid fiberglass which will maintain the shape of the steel beam.
When we have two of these completed, then we will add two more layers of fiberglass cloth and epoxy between them and set them back-to-back. This will give us an I-beam shape that will have the rigidity required to support the floor of the SeaPod.
We have also done a few extra tests using a diagonal fiberglass cloth. The single layer of cloth here is fairly flexible. The double layer is considerably more rigid. And the cloth that we have been using falls right between these two when it comes to flexibility.
So, we will take these test pieces and turn them into I-beams so that we can compare them with our current method to determine which option will fit our needs the best. Be sure to follow along for more updates as the SeaPod production sails on!