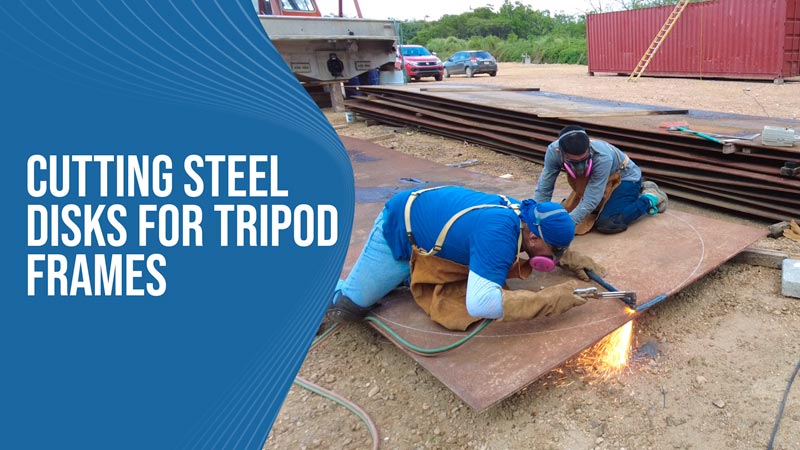
We have a steel disk that creates a bit of a flange on the bottom of each hub on our floating TriPod bases. The hub is what we call the center spar where the three outriggers are welded together. This “caps off” the bottom of the hub and helps seal everything up while giving us a flange to work with as well.
Unfortunately, steel comes in flat sheets that are either square or rectangle so we have to cut the circular disk shape from a square sheet of steel. This steel is 12mm thick so we are using a torch to cut it. We can’t freehand the cuts since we need the disk to be a perfect circle so we have a jig that gives us the perfect cut.
The jig works similarly to a compass that you may have used in math class to draw a perfect circle. We first use the jig with a piece of soapstone to draw our circle on the surface of the steel. Once we have our circle, we swap the soapstone for our oxy-acetylene torch and get to cutting.
After we cut the disk out of the square sheet, we have to clean up the edges so that everything is smooth and is free of any deformities that may have happened during the cutting process. Once we have the disk, we can weld it onto the bottom of the hub where it will permanently live. This process is followed by sandblasting and applying the surface protectant to keep the metal protected from corrosion.
This jig allows us to quickly and reliably cut these disks which is very important since we want to reduce the production time of every aspect possible so that we can build SeaPods faster and faster. Be sure to follow along as we continue to progress toward getting the SeaPod into production.