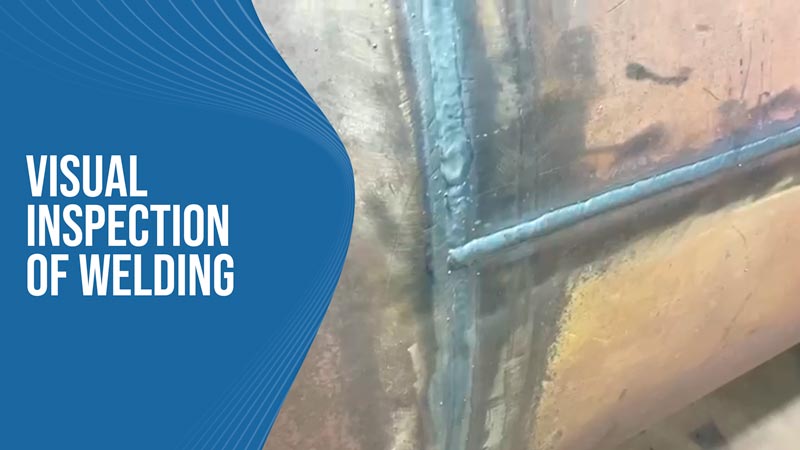
We are beginning to ramp up the production of our second and third SeaPod bases. The first base that we built will be used in our show home as an example of what the SeaPod will be, but these next two bases are the start of the actual production of SeaPod homes.
We feel much more comfortable with our construction process after all of the trial & error of building the first base. As we move through the construction process, we are constantly inspecting everything to ensure that there are no loose ends that are left during the production.
The main structure of the SeaPod is made from steel tubes that are welded together. Something that many people don’t realize is that we are making our own steel tubes. When we receive the steel, it comes in large flat sheets that we cut to size put through a rolling machine that bends the flat pieces into the round tubes.
After the bending is complete, we have to weld the seam to give it strength. Along with welding the tube sections together, each one has a welded seam from this process. Even though we have very talented and skilled welders, we still inspect every single weld that is made during the production process.
Even the best welders can make mistakes so it is important for us to double-check everything since this steel is what supports all of the weight of the SeaPod. We use several methods of inspection but the first and quickest is a visual inspection.
We start by looking at every weld to make sure that there is nothing that immediately stands out. While this seems almost too simple, it is an important part of the process. We have some more in-depth methods of testing that we also do but the visual inspection allows us to catch and correct anything obvious before we bring out the technology.
We will have some more updates coming soon that explain some of our other methods for testing these welds. We are hard at work here at the factory and we hope that everyone is enjoying following along as we move into the production of actual SeaPods!