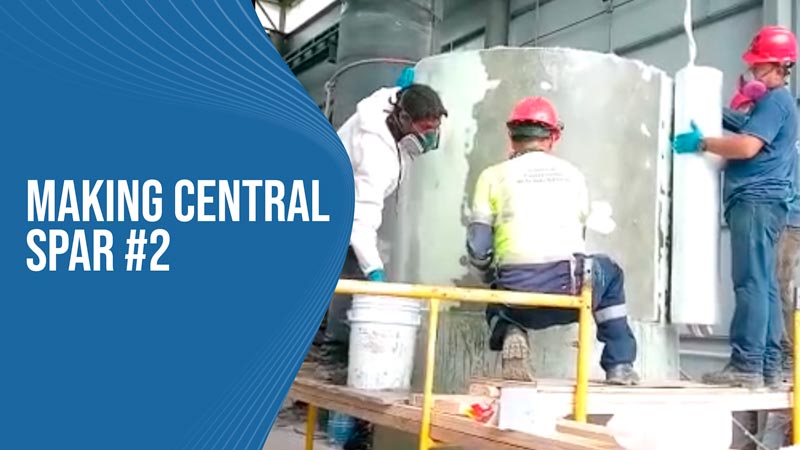
We are back at the factory with an update on the construction of our second SeaPod central spar. You can see the team working on applying the fiberglass layers and resin to the structure. What we are working on here is essentially a fiberglass collar or sleeve that will go over the internal steel spar structure. The layers of fiberglass are wrapped around the center shape which acts as a mold to give us the shape that we need.
The previous one that we made was about eight meters tall and several centimeters thick. For this one we are adjusting our process a little bit. Instead of making the entire piece have the required thickness from the start, we will make it much thinner. Then once we have it positioned with the SeaPod molds fitted where they need to be, we will go back and add more fiberglass in the places where it is needed for strength.
We will reduce our material waste by doing the process this way. When we cut the doors and windows out, we won’t have to cut out a section that is the entire thickness of the piece. Since we are only applying the additional fiberglass where it is needed, we won’t be wasting fiberglass layers on areas that will be cut out and discarded anyway.
This process won’t compromise the strength of the structure, it will simply allow us to use our materials more efficiently. Fiberglass is layered on and hardened with epoxy so we can change the thickness of the fiberglass by simply adding fewer layers of the fiberglass cloth that comes on these rolls. We can then go back and reinforce the areas that require a bit more structural strength.
Saving materials is very important, especially during this time when we are doing a bit of experimentation and research with our process. In addition to our mission of living a less wasteful life in general, we can save materials and money during these stages of development which will make the entire process of bringing the SeaPod to life more efficient.